Flexo printing pays attention to the setting of various parameters from the beginning of printing. As long as the parameters are set consistently, the printing effect of each batch of orders can be basically the same, which is very different from other printing methods depending on the experience of the captain. .
1. Establish standards
Digital management must first have printing standards, target-oriented, and select or customize printing standards according to the requirements of customers or products themselves. In general, we will select the major printing industry standards that all ICC color profiles can be downloaded from the Internet and have been released. Of course, you can also set your own corporate standards. Large printing groups generally set their own printing standards for each printing company within the group based on the Group's main products, paper, ink and other conditions.
2. Get raw data
According to the company's existing printing conditions the printing blanket standard ISO 12647 FOGRA39 test strip, then the application Xrite EyeOne densimeter correlation measurements, to obtain the ink used and the printing screen Lab parameters like dot data expanded.
3. Compare with standard data
The measurement data is imported into the French color source CMYK field software, and the current printing data can be compared with the standard data selected by the enterprise to guide the adjustment and specification of the ink, including:
(1) Compare the printing color gamut and the target color gamut under the current printing conditions, as shown in Fig. 1.
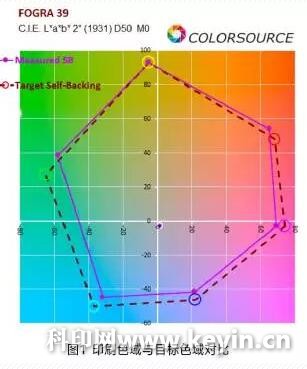
(2) The measured four primary color ink concentrations, Lab values, and target values ​​are compared to determine adjustments and adjustment ranges. In the four primary color inks used in this case, the blue ink needs to increase the ink density from 1.1 to 1.25 to reduce the chromatic aberration to the standard range, as shown in Figure 2.
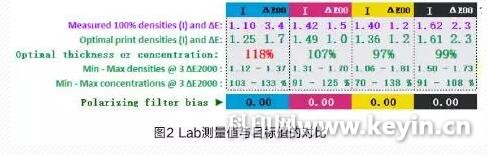
(3) Data comparison when RGB field and CMYK different dot percentages are performed. In this case, due to the influence of the green ink, the green yellow will not meet the standard requirements when it is green, as shown in Figure 3 (the green block is highlighted with a red underline).

4. Ink normalization
Due to the differences in paper white (substrate), CMYK Lab values ​​may vary. Based on the previous data comparison, the software can guide the operator through adjustments to ink concentration and printing conditions (pressure, anilox roll configuration). To achieve the best Lab value (the smaller the ΔE value, the better the flexo ink, whether it is ink or UV ink, and the chromatic aberration of the offset target value should be maintained between YMC 0.5~2, K2~3.5, so that the ink can be made The hue is as close as possible to the standard ink hue.
5. Measuring the expansion of outlets
After standardizing the ink field Lab value, a standardized printing test strip is printed again, and the measured data is imported into the French color source ColorSource curve creation software to obtain the dot enlargement data and curve under the current printing conditions, and the red color in Fig. 4 The line is the current printing dot expansion curve, and the deep red dotted line is the dot expansion target curve. According to the data and curve expanded by the Internet point, the gap between the current Measured and the Target Curve can be judged, and the size of the dot at the time of plate making can be adjusted to narrow the gap between the two. difference.
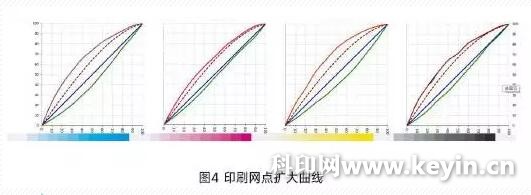
Makeup Tools.Best Shaving Brush,Shaving Brush Kits,Shaving Brush Kit,Shaving Brush And Bowl,Beard Brush
Shenzhen Nanfang Shishang Cosmetic Utensil Co., Ltd. , https://www.sznfssmakeupbrush.com