With the rapid development of information technology, computers and graphic processing technologies are increasingly popularized and popularized, and the printing industry is constantly undergoing a transition from analog production methods to digital workflows. In recent years, computer to plate (CTP technology) has become a hot topic, and flexo direct platemaking (generally referred to as "digital flexo") technology is also available in the packaging and printing industry. The rapid development, and won the user's approval with high quality. However, some people still think that it is inappropriate to call such a flexographic platemaking technology a “digital flexoâ€. Kenny Lennox is one of them. Not long ago, he also wrote an article specifically to discuss this issue, but also made a full argument. First, "digital" and "analogue" "digital" is relative to "analogue". Basically, digital information comes from the material world that we gradually recognize. For example, as we all know, the effect of listening to music on a digital CD player is different from that of live broadcasting. The reason is that digital, computer-based, digital-to-analog information is used in discs, disks, and CD players. The order of the arrangement is not the same as that of things. After we have to convert digital information into analog information, we can correctly understand the meaning and significance of things. If the CD player is unsuccessful in decoding, a series of distortions will occur. After the originally recorded music on the CD player is played out through the speaker, the sound quality will decrease. Although it is possible to include "surround stereo" in the analog workflow (in digital workflows, "surround stereo" sometimes suffers from intermittent and unsmooth issues.), but to a certain degree of quality loss, this is a simulation job. One of the inherent characteristics of the process. Second, the relationship between digital technology and flexographic printing Not long ago, everything is still simulated, which is one of the reasons for the decline in quality, so people are very anxious. Later, with the digital prepress workflow and a series of standardized adjustments and calibrations of the collator, the error rate was greatly reduced to some extent. At the same time, anilox rollers and inking systems have also been greatly improved. Therefore, these advantages can be utilized in later printing processes. Nowadays, the flexo plate-making process is no longer the era that used the rubber plate. Its product quality can be comparable to gravure printing. In a word, the flexo plate making technology has gradually abandoned or improved the traditional simulation production process after experiencing many difficulties and setbacks (for example, the early digitized workflow adopted the dot matrix or jagged image). Take us into a new era. What does the so-called "digital flexo" technology mean? It abandoned the film (including exposure, development, fixing and a series of corresponding processing procedures), saved the simulation process, replaced by another simulation process - laser ablation imaging. The principle of laser ablation imaging is that there is a layer of coating on the photosensitive layer of the plate. When making the plate, the laser from the laser generator of the plate-making machine ablates the coating of the image part, exposing the underlying photosensitive layer. Then, the printing plate is exposed. In the non-graphic part of the printing plate, photopolymerization does not occur due to the coating blocking the light (functioning as a mask), and the photosensitive layer of the graphic part undergoes photopolymerization. , thus forming a printing outlet. This imaging method is no more "digital" than the previous imaging methods. Why? The reason is that as soon as the digital information is transmitted to the laser, the digital production process of printing and copying is completed, and the subsequent work is still simulated. This is true whether you are using film or CTP technology. If one simply thinks that "as long as it is digital, it is good," this view and mode of thinking will be too one-sided and extreme. The advantages of the direct platemaking technology lie first in the simulated UV exposure, especially the characteristics of the UV light source. The new plates used in direct platemaking technology do not contain any more digital technology at all. For offset printing, flexo printing, or other printing processes, it has never experienced such a major breakthrough as "computer-to-plate technology." Therefore, using such a term to describe it is difficult for others to understand its meaning. . Just like many new things in the past decades, the new CTP technology does not require much skill, it is almost "fool-type", and this is exactly what it wins. Recently, the relevant organizations investigated a number of platemaking companies and measured the accuracy and quality of their output films. The results show that most companies are not optimistic about the situation, especially in the most sensitive high-light areas of flexographic printing. Therefore, quality awareness should be strengthened. Because there are various non-standardized operations in the traditional process, the direct platemaking system replaces the manual operation with a machine, the performance is more stable, the error is smaller, the error probability is lower, and the quality is more reliable, which is also an advantage of the new process. However, the promotion and application of new processes also require a process, and exposure calibration is still very important. Next, the second step is to expose the plate with a UV plate. This step can also reduce the drawbacks of the simulation process. As we all know, when a conventional ordinary flexographic plate is exposed, the film is not in close contact with the plate. Ultraviolet rays must pass through the vacuum layer, the film base, the emulsion layer, and the anti-halation layer, and there are more serious scattering and scattering. In the reflection problem, the edges of the resulting dots are not clean, irregular, and have uneven density, and the quality of the final printed matter will be correspondingly poor. If the direct plate making technique is adopted, there is no such problem, and the UV light source is more stable, resulting in smaller dot sites and easier control. High-precision is one of the advantages of direct platemaking technology. In addition, most of the research results have proved that: the dots produced by direct plate making technology are of complete dot type and extremely high optical dots, which are not easy to lose, and they also have small dot gain and order in the printing process. Tuning, large outlets do not paste and other advantages. The ordinary printing plate used in the traditional process will produce a small dot gain during the exposure process, but this fact has hardly been heard in most of the discussions.
About us:
We have advanced production equipment and phone cases molds manufacturing equipment, and improved the quality control system and humane management system.
We brings together a group of elite Chinese talent in the industry, technology and management, as we develop, produce each product delivered to the customer, providing a very reliable quality assurance!
What we have:
â—‹ area of 15000 square meters with 500 employees
â—‹ more than 44 injection machines, 10000 Class dust-free spray paint workshop
â—‹ advanced technology and considerate service
â—‹ fashion design and reasonable price
About Imd iphone7 plus case:
IMD is in mold decoration technology, IMD is the international popular surface decoration technology, surface hardening, transparent film, intermediate printing pattern layer, middle layer on the back of injection molding, printing ink, can make the product wear resistance, prevent surface scratches, and can maintain long-term bright color is not easy to fade.
We have richful sources and experience in dealing with iml iphone7 plus case.
This Popular Imd iphone7 plus case series divide into many designs and many styles. This material of Clear Picture Print IMD iphone7plus cover has good flexibility and toughness, soft hand feeling.
Others advantages for Imd iPhone7 plus case are flowering:
1. Eco-friendly and dust prevention;
2. High and low temperature resistance, weather resistance;
3. Excellent electrical insulation property and water repellency;
4.Decorate your own cell phone, make it more fashionable;
5.Protect your cell phone from scratching and shocking;
6.Easy to install and remove
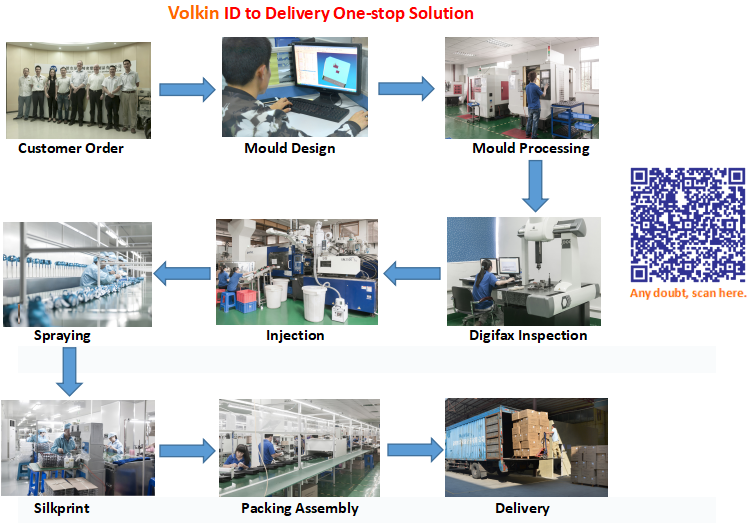
About package and shipping
Each pc in one bag or Packing According to customer requirement.
.Door to door service for small cargo.
The products will ship out within 7 working days after confirmation of payment.
The tracking NO will be emailed to you once we have shipped your order.
Contract us
Shenzhen Volkin Technology Co., Ltd.
Quality Is Our Culture
Imd Iphone 7 Plus Case
Imd Iphone 7 Plus Case,Imd Iphone 7 Plus Case,Imd Iphone 7 Plus Cover,Iml Iphone 7 Plus Case
Shenzhen Volkin Technology Co., Ltd. , http://www.canicase.com